Zipping And Floating: Or How To Remove A Ponderosa From Someone’s Roof
This was an interesting one. I’ve been blessed to have some very cool technical removal experience in my past, but this one really took the title for most complex removal I’ve ever attempted. I have to thank everyone who trained me for helping me arrive in a place where I could even conceive of how to get this one done safely. I also have to thank my awesome crewman, Tim, for his cool head and open eyes.
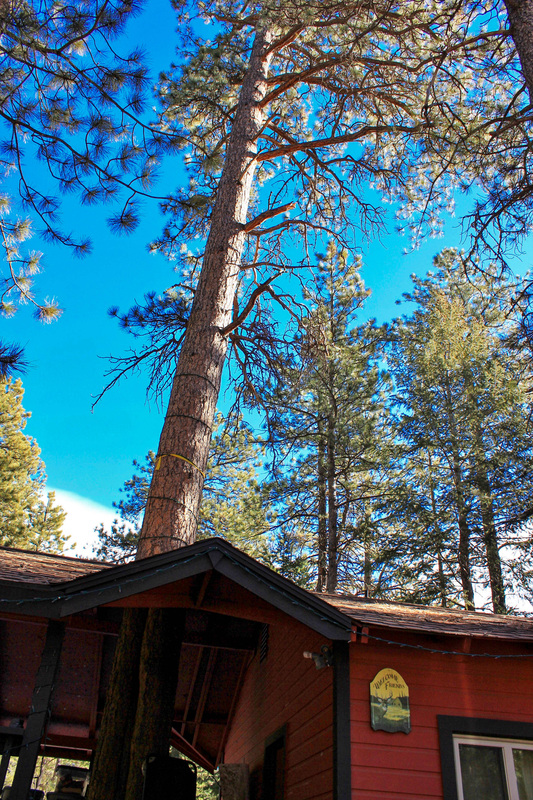
That, friends and colleagues, is a 26″ diameter Ponderosa Pine stem through the roof of a patio outside of Evergreen, Colorado.
Hmm. Presents a bit of a conundrum, doesn’t it?
There’s not much of a drop-zone here. The roof extends on all sides of the tree a minimum of 15 feet, and the tree is in the exact peak of the roof. Lengthwise, the shortest distance from the stem is 20 feet.
I would have loved to have used a crane, but the cabin in question is on a hillside and the only remotely flat ground nearby is a septic tank and leech field. Hmm.
Bucket truck? The stem was a good 70 feet tall from the base, and the pieces of wood near the bottom weighed close to 300 lbs for a 24″ section. Assuming you could get a truck close enough to work from, that’s not exactly the kind of weight bucket truck manufacturers like to see lowered from their man lifts.
The solution (you all knew this was coming) was rigging. Creative, careful, adaptable rigging!
Phase one was a mobile zip line from the trunk of the tree to the ground below. Tension was managed using a friction based lowering device by Buckingham called a port-a-wrap. The line was held taut as the pieces fell onto slings attached to auto-locking carabiners. As the piece rode closer to ground and clear of the roof, the line tension was released, allowing for a smooth, controlled landing.
We successfully dropped all the Ponderosa’s limbs as well as a large amount of the stem onto the zip line without coming close to hitting the roof directly below. All of our material landed about 30′ away from the building, in fact, which I counted as a major win.
Phase 2 was much more complicated. This tree was the largest in the immediate vicinity. Everything nearby was much smaller, much shorter and much less stocky. Nevertheless, we needed a place to put our lowering point to get the large pieces of the stem off of the tree. In a normal situation, it would be easy enough to catch most of the wood on the stem itself by fixing the block below the cut. In this case I wanted to be as certain as possible that the 300-pound or more pieces of green Ponderosa Pine would fall clear of the roof-line. I didn’t trust that once I got within 15′ of the roof I would be able to stop the wood from smacking it. One good tap had the very real potential to add up to repair costs that would have far exceeded my fee for performing the work.
This was one case where “close enough” was definitely not going to cut it.
So we got crafty. I used two of the smaller adjacent trees as anchor points for a tyrolean traverse of sorts. We set a high-line and tied an alpine butterfly knot to anchor our lowering block effectively in mid-air. It took lots of patience, moving the block often to find the best location and adding as much tension as possible to the system -the whole time trying not to risk breaking the tops out of the anchor trees.
Doing the job of a crane without using a crane is clearly very risky business. The variables we were juggling included the amount of stretch in two large diameter rigging lines -one 1/2″ and one 5/8″, the amount the floating block would dip under load due to the two anchor trees bending together, and the location of the block over the house changing as the ropes and trees stretched. This is where Tim’s clear head was indispensable. Impatience during planning time could easily have led to something being missed. Missing something would almost certainly have meant a 300 pound piece of wood in the kitchen sink.
he floating block worked exactly as we intended it to. We were able to get the trunk to within 8 feet of the roof line, and then used it (with applied mechanical advantage on the lowering line) to get the remaining portion of the stem felled without punching a hole in the roof. The two day operation was an incredible success, and we proved that you don’t need heavy machinery or a helicopter to deal with complicated situations like a tree growing through a roof. What you DO need are rope and rigging skills, a very calm and efficient team, clarity and a heaping portion of patience.
This job was a real test for everyone involved, but the feeling of accomplishment at the close of day 2 was pretty incredible. We’d gone from a 70 foot Pine in a horrible location to a stump right at the roof line. Most importantly, there had been zero damage to the property, and both Tim and I were able to go home safely at the end of the project with nary a scratch. These kinds of jobs can be stressful, and they involve a lot of planning and thought well in advance, but when they go well it’s all worth it. I was so happy at the end of the day to be able to tell my client the tree had come down and the house was still intact!
BIG thanks to Devin Chamberlain for the photos from Day 1, and even bigger thanks to Tim Davis for being a great rope runner and a standup guy!